Safety in assembly machine with rotary table – ReeR Safety
Assembly Machine with Rotary Table for Hinges of Armored Doors.
TECNAS Srl, which has been in the assembly machine business for years, has chosen ReeR Safety technology and devices to ensure operator safety and maximize efficiency during the production process. The complexity of regulations, the variety of products and the specific needs of customers require close and continuous collaboration between the machine manufacturer and safety solution providers. ReeR Spa, thanks to its participation in the main national and international committees on machine safety, is the ideal partner to meet any safety-related application needs. An example of this collaboration is the safety system built by ReeR Spa on the assembly machine for the assembly of hinges for armored doors of TECNAS Srl.
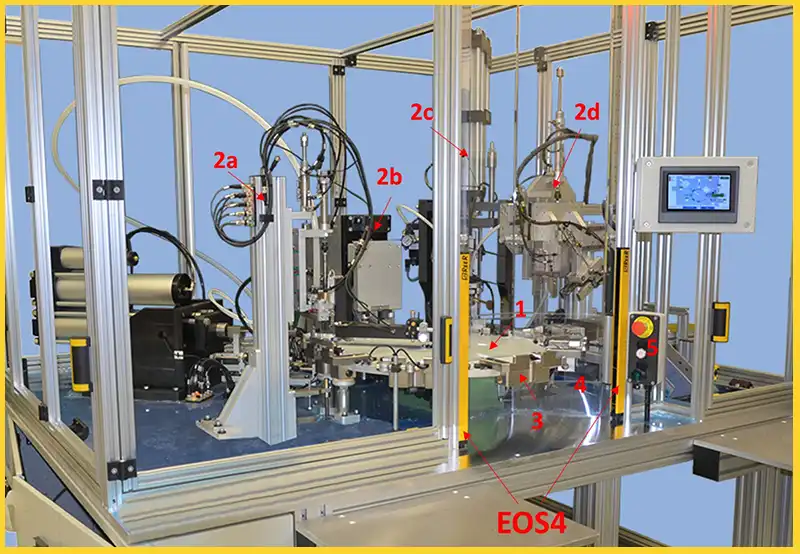
Assembly machine operation and safety challenges
The hub of the assembly machine consists of a rotary table [1] that moves the workpieces between the various workstations [2a, 2b, 2c, 2d] by means of a carousel motion until the complete hinge is obtained. With this type of machine, interaction between the operator and the machine occurs only in the phase of loading the semi-finished product into the appropriate compartment [3].
Operator protection is provided both in the purely operational phase by:
- A plexiglass bulkhead as physical protection [4]
- An immaterial barrier realized by means of a ReeR EOS4 453 X safety light curtain (Type 4 safety barrier, length 450 mm, hand resolution).
That in control or maintenance ones by:
- Transparent side access doors to individual workstations.
During the operational stages of each workstation, the operator can press the start button [5], activating table rotation. The plexiglass bulkhead rises to allow rotation, and then lowers to allow safe loading by the operator of the workpiece. During this loading phase, the safety barrier is temporarily deactivated to facilitate the process. When the bulkhead is up, ReeR Spa’s EOS4 safety light curtain remains active to immediately stop the machine if it detects the presence of an object, ensuring operator protection.
In relation to machine operation and regulatory and operational requirements, the main safety challenges to be addressed are:
- Safe control of the plexiglass bulkhead
- Verification of the positioning of the rotary table
- Management of the activation and deactivation of the safety barrier
- Safe control of the side doors
ReeR’s solution for safety in rotary table assembly machines
Verification of rotary table and bulkhead position is provided by PI-SAFE inductive sensors that offer safe, non-contact detection of metal objects, as required by EN 60947-5-3, IEC 61508 and ISO 13849 standards:
- Two PI-SAFE sensors monitor the position of the bulkhead by detecting the proximity of metal blocks located on the side of the bulkhead: one for the open bulkhead position and one for the closed bulkhead position.
- A PI-SAFE sensor monitors the position of the rotary table by checking the position of a metal block placed on the axis.
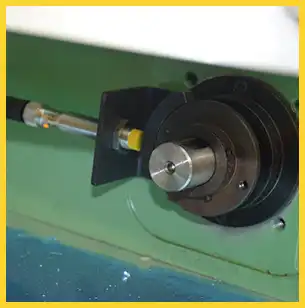
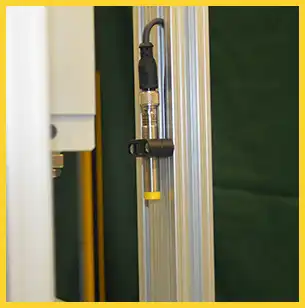
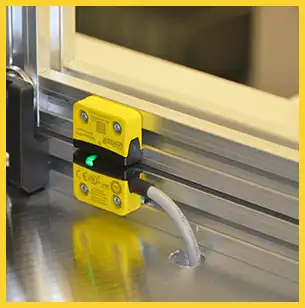
The closed bulkhead and stationary rotary table lead to a disabling of the barrier, allowing the operator to load a new semi-finished product into the rotary table compartment. With the bulkhead open and the rotary table in motion, the barrier is enabled and stops the machine in case an object is detected.
Operator safety is further ensured by MAGNUS RFID sensors, which verify that the side doors are closed. Accidental opening of a door results in the immediate stopping of the machine, preventing risks to the operator.
ReeR Solution
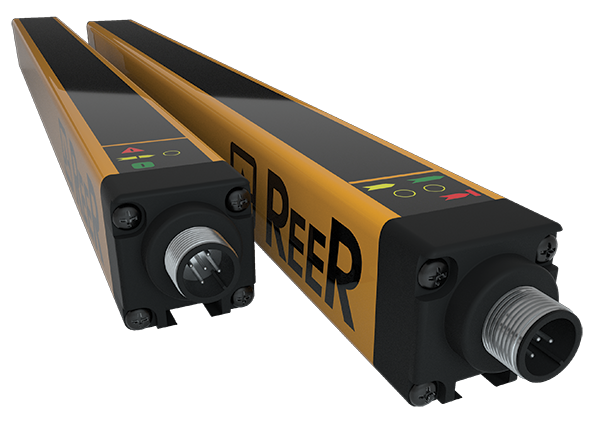
EOS4 Safety light curtain
Hand Detection Safety Light Curtain with Automatic/Manual Restart and EDM
EOS4 453 X:
- Safety level: Type 4 – PL e
- Resolution: 30mm
- Protected height: 460 mm
- Cross Section: 28 x 30 mm
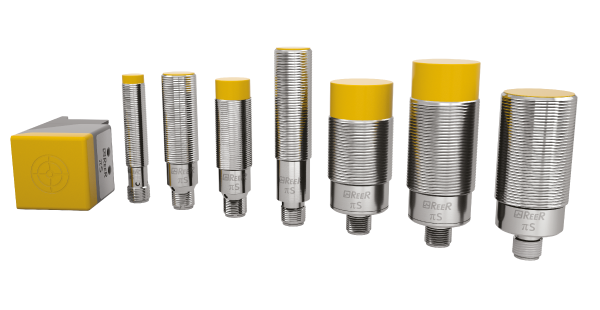
PI-SAFE Safety sensors
Fail-safe inductive sensors for position detection
- Safety level: PL d
- Sensor type: Inductive sensors
- Switching distance: 0.5…5 mm
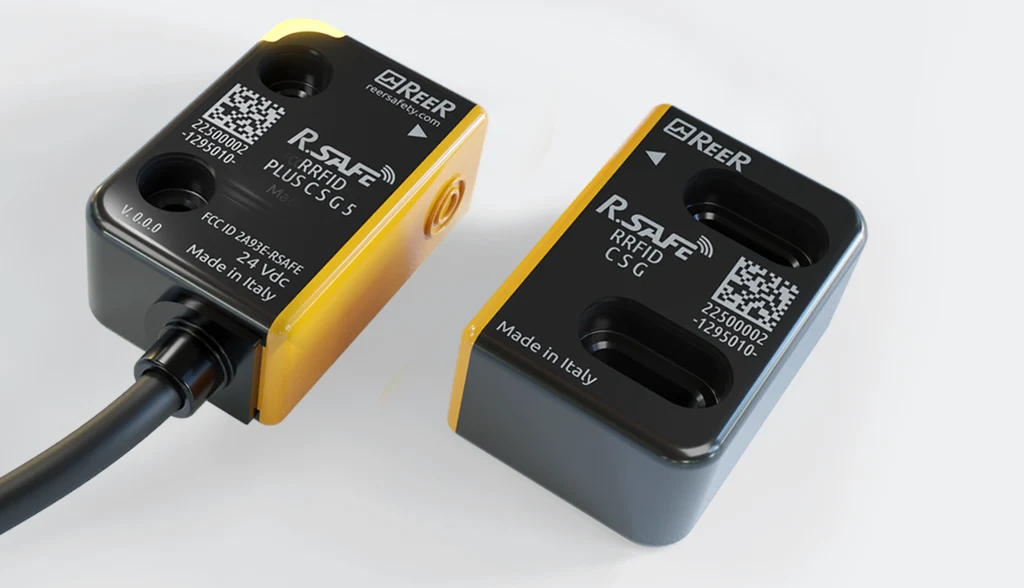
RFID Safety sensors
Safety switches for position control of movable guards.
- High visible status LED
- RFID technology
- Anti-tampering protection caps
MOSAIC Controller for Modular Safety
MOSAIC is the safety controller that is a modular and configurable solution, adaptable to various functional parameters such as timings, inputs, outputs and more.
In this application, an M1 Master Unit and MI8O2 I/O Expansion Unit were used to control both the sensors and all the activation and deactivation logic of the ESO4 safety barrier.
Both Master Unit M1 and Expansion Unit MI802 are manageable through the MOSAIC Safety Designer (MSD) software.
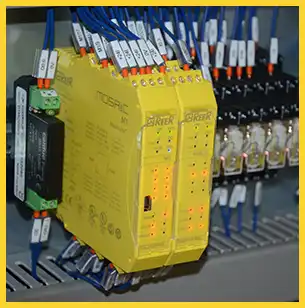
ReeR Solution
Safety Controllers and Interfaces
Mosaic is a safety hub able to manage all safety functions of machinery. Configurable and scalable, provides cost reductions and minimal wiring.
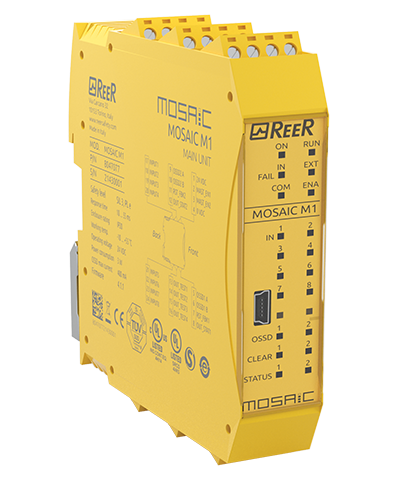
MOSAIC M1
- 8 Inputs
- 2 OSSD pairs (SIL 3)
- Screw terminal blocks
In this application, additional input/output are given by the expansion unit MOSAIC MI802, with:
- 8 digital inputs
- 2 inputs for Start/Restart interlock and external device monitoring (EDM)
- 2 pairs OSSD safety outputs
- 2 status outputs
- 4 test outputs
Protect Your Machines with ReeR Safety.
If you’re looking for reliable, modular solutions for the safety of your machines, ReeR Safety is the ideal partner to meet the challenges of operator protection and position and motion control. Contact us today to find out how we can improve the safety and efficiency of your assembly plants.
ReeR, your future’s safe!